During welding operation, a digital control arc welding machine is designed to be responsive to the welding process. Digital controllers may include features that improve control and reduce the amount of time the controller needs to respond to changes in the welding process. This may be achieved by modifying various controller coefficients and compensation functions. It may also be configured to dampen the effect of induced voltage on the voltage feedback signal due to weld cable inductance.
A digital control arc welding machine may also be able to control the waveform of the current flowing through the welding arc. This is achieved by modifying the current waveform shape as well as other characteristics of the current. This may include controlling the reference current and lower and upper limit current levels. Depending on the welding process, the current waveform may be optimized for the best efficiency and performance. Some processes involve low output currents and may require a higher switching frequency to achieve the best performance. The resulting lower duty cycle may reduce thermal stress on power components.
A digital control arc welding machine can use measured or calculated inductance values for control purposes. The controller may use this information to compensate for the voltage feedback signal, dampen the ringing effect of the voltage feedback signal, or use it as a warning signal to the operator when the inductance is too low. This information may also be used to modify various control loop system parameters.
The controller may also calculate the duty cycle for the welding operation. This may be based on digitized values of the waveform or by multiplying the output current rate by the calculated equivalent cable inductance. The controller may also modify the coefficient terms K1-K5. This may be achieved by modifying the compensation functions. In addition, the controller may use additional signals to calculate the duty cycle. These include the bus voltage, the reference current, and the bus voltage feedback. The controller may also calculate the droop term, which accounts for the non-ideal transfer function of the welding power supply.
The controller may use the voltage feedback signal to clamp the feedback voltage to a preset value. The value of the feedback voltage may be clamped to a level that is greater than the typical arc voltage. This may provide a fast dynamic response.
A digital controller may also be used to modify the coefficient terms K1-K5. These terms may be modified based on the welding arc impedance and other factors. The controller may also be configured to calculate a lower duty cycle term or the upper limit duty cycle term. This may be achieved by modifying the coefficient terms or modifying the switching frequency. This may allow the controller to reduce the amount of arc outage and improve the welding process.
Other aspects of a digital control arc welding machine may include a closed current control loop that allows the power supply to operate as a controlled current source. This may include an inductor that smooths the output voltage and provides smoothing of the output current. The inductor may be a smoothing inductor that is internal to the power supply.
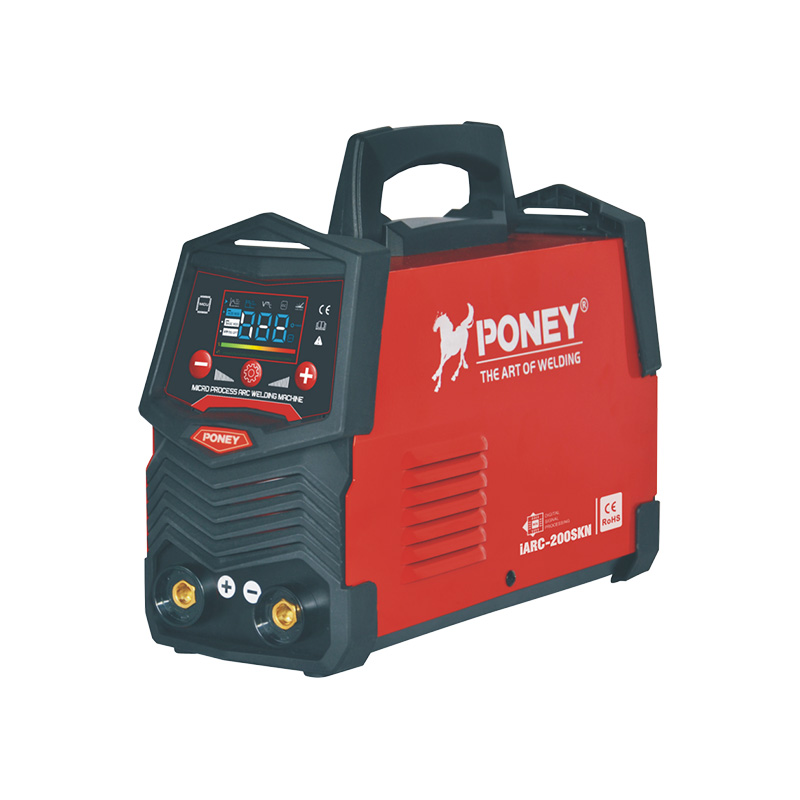
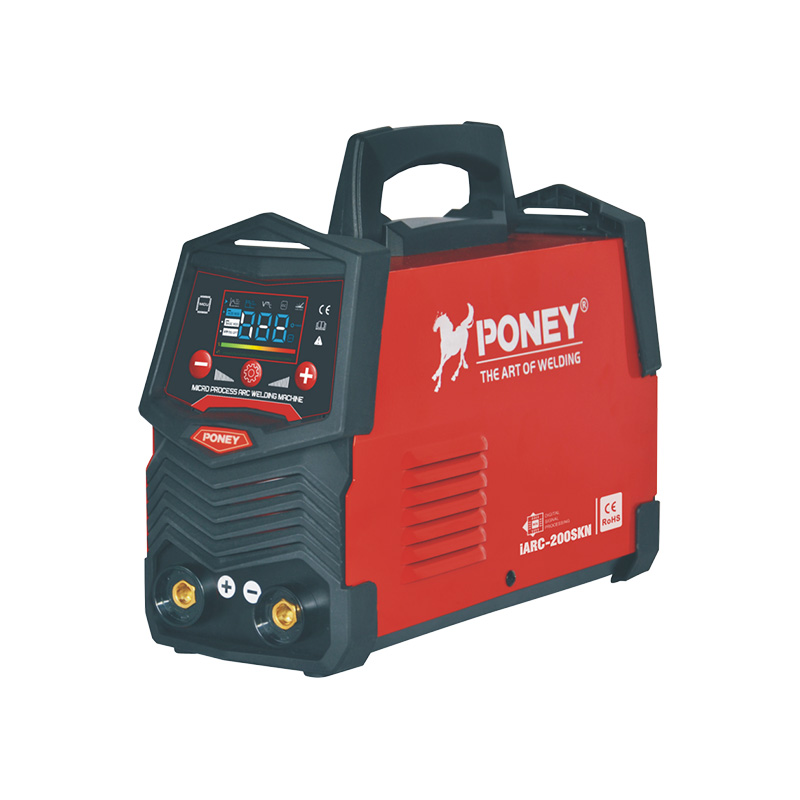
This intelligent arc welding machine uses digital signal processing welding technology . it features anti stick , arc force , hot start , VRD , short circuit protection , and sleep mode . 2.5” digit display is used . able to weld MMA and TIG lift for different metal works welding . Dynamic response , smooth and stable arc makes this welding machine the most wanted welder , that widely used DIY , workshops , home use . etc.